Cutting Energy Costs with Inverters
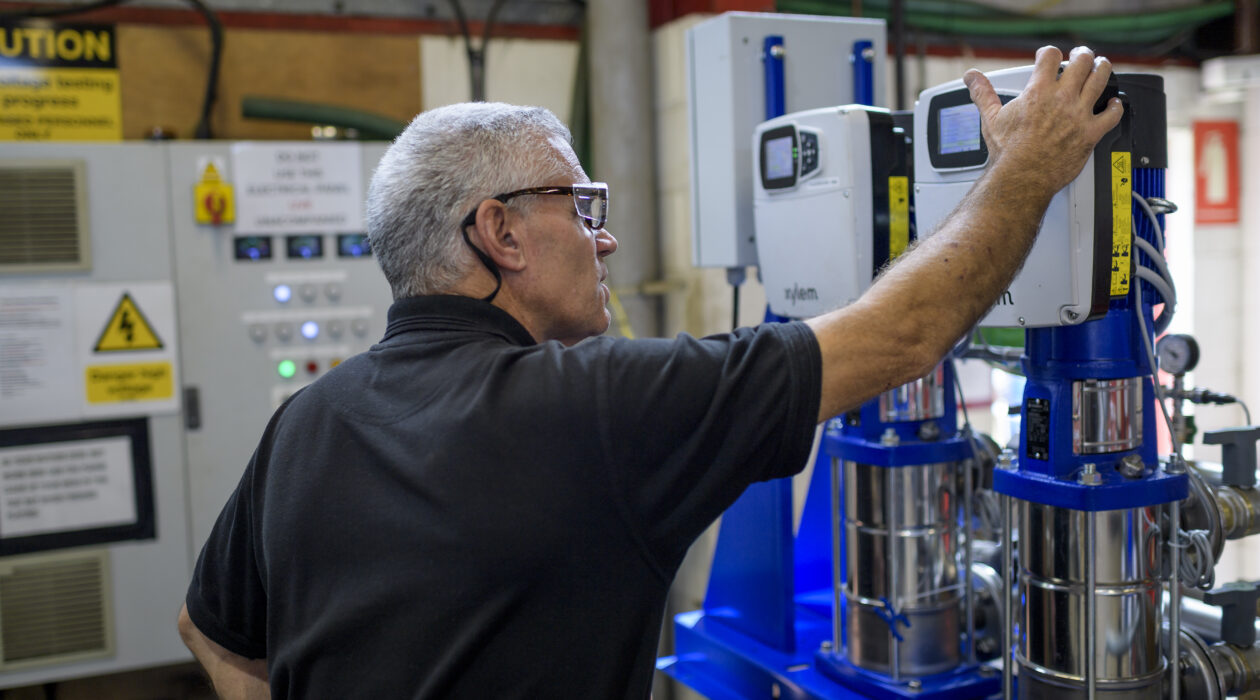
Anglo Pumps are able to assess and evaluate methods for a reduction of carbon emissions and increased energy efficiency in plant rooms and at pumping stations.
There are various approaches used to control the flow rate of a pump, but they all come with their own inefficiencies. However, there are tried and tested solutions for efficiently managing the performance of pumps in the form of inverters or variable frequency drives (VFDs).
Pumps with inverters are more energy efficient because they provide variable flow rate control that delivers energy efficiencies during operation, and are intrinsically more efficient because of the affinity laws, where running a pump motor at lower rates reduces energy consumption by a significant percentage. A 25% decrease in pump motor speed can reduce energy consumption by as much as 60%.
The problem:
- A customer running a 7.5KwH pump that cost £4,600, consumed over 65,000 KwH annually. The energy bill was over £19,000 per annum.
The solution:
- Anglo Pumps installed a 7.5KwH inverter at a cost of £7,500.
- Coupled with appropriate sensors and transducers, the inverter-controlled pump motors provided pumping power according to the demand requirements of the system, rather than at either peak operating output or at a suboptimal and lower efficiency output.
The benefits:
- The inverter reduced energy consumption by 30%, cutting the yearly energy bill to under £14,000.
- The return on the investment was realised within 16 months, and over the 15-year life span of the system, expected to save the customer over £80,000.
- Running the pump motor with soft starting and stopping, less strain was placed on the motor and the wider system, protecting seals, joints and pipelines.
- The mechanical elements of the motor will run smoothly without additional friction and wear.
Heat Exchanger:
- Two-week project including the design and installation of two hot water calorifiers and replace with new plate heat exchangers
- Exchanger units able to cater for abnormal/intermittent peak demands.
Benefits:
- Upgrade of existing equipment to new, more energy efficient units, but still able to accommodate peak demands.